本記事の内容
はじめに
私は、メーカーで製造現場にAIを実装する仕事をしています。
設備のセンサーから取得したデータを活用して、機械学習を用いて外観検査を自動化したり、設備の異常検知の為のアルゴリズム開発を行っています。
しかし、設備データの保管場所がサイロ化していたり、特定設備・プロセスのためのアルゴリズムになってしまったりと、効果のスケールアップが難しいと日々感じていました。
アルゴリズム開発をしていると、日頃、統計解析や機械学習の手法の細部の議論をすることが多いです。技術を深堀することは必要ですが、「木を見て森を見ずになっているのでは?」との気持ちがありました。
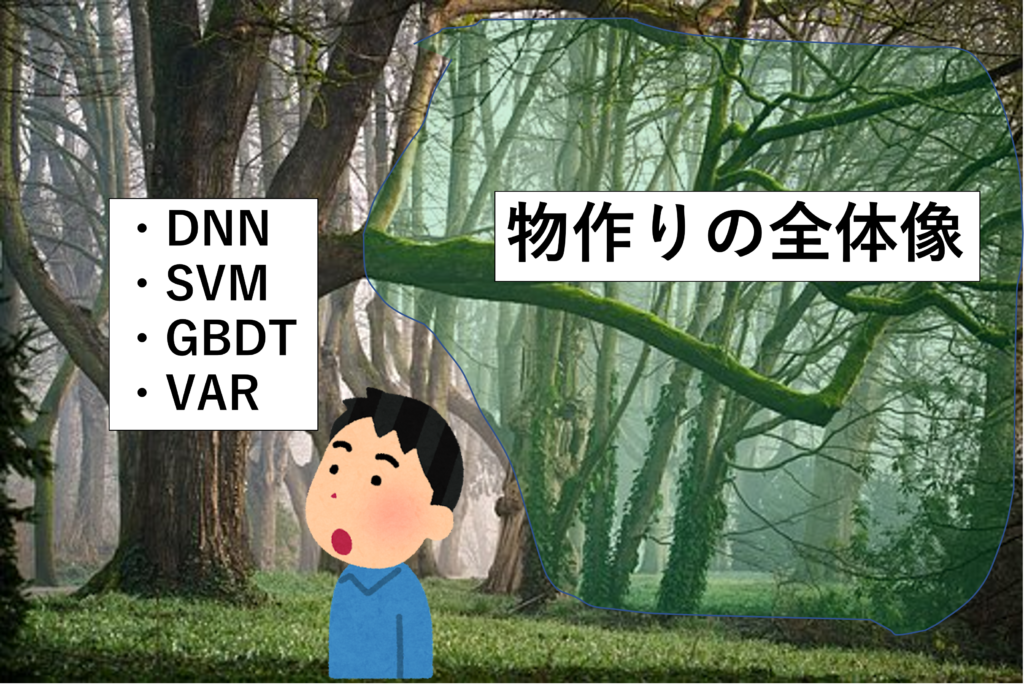
木を見て森を見ず
そんな折、以下のツイートをきっかけに物作りを俯瞰的に考える必要があるとの気持ちが湧いてきました。
そして、物作りを俯瞰的に捉えるために、ISA-95というフレームワークが有用であることを知り、勉強してみることにしました。勉強するうちに、製造業 × DXを考える上で必要な知識だと思うようになりました。
SNSで、私が普段仕事をしている高度と違う方々との出会いがあるのは、とても刺激になる。
ツイッターでは。ものづくり高度100mの方と、そしてリンクトインでは昨日高度1000-10,000mの方と話しをさせてもらった。
仕事や視点が違うから、対話させてもらうと気付きがいっぱい得られるんですね。 pic.twitter.com/eUgBxiJCIT
— おかさん Minoru OKA (@okappiki3) November 20, 2021
この記事を書いた人
データサイエンティストにキャリアチェンジした元生産技術者です。
(宜しければ、プロフィールをご覧ください)
ISA-95とは
International Society of Automation(ISA : 自動機器に関する国際的な標準化団体)が定めた物作りに関わる情報システムのための標準化規格です。
規格がない or 準拠しない場合、経営管理システムと製造管理システムの連携が困難になることが予想されます。
ISAでは、活動範囲と目的を以下のように定めています。
Scope
- Multi-part effort
- Define in detail an abstract model of the enterprise, including manufacturing control functions and business functions, and its information exchange.
- Establish common terminology for the description and understanding of enterprise, including manufacturing control functions and business process functions, and its information exchange.
- Define electronic information exchange between the manufacturing control functions and other enterprise functions including data models and exchange definitions.
Purpose
To create a standard that will define the interface between control functions and other enterprise functions based upon the Purdue Reference Model for CIM (hierarchical form) as published by ISA. The interface initially considered is the interface between levels 3 and 4 of that model. Additional interfaces will be considered, as appropriate. The goal is to reduce the risk, cost, and errors associated with implementing these interfaces. The standard must define information exchange that is robust, safe, and cost effective. The exchange mechanism must preserve the integrity of each system's information and span of control.
英語が得意でないので、あっているか分かりませんが、要約すると、以下のようかと思います。
ISA-95の範囲と目的
ISA-95の要点
ISA-95については、参考資料に分かり易くまとまっているので、詳細は割愛します。これらの資料は、日本語で書かれた資料としては一番分かり易いと思いまうす。
ISA-95を勉強されたいかたは是非、読んでみる価値があると思います。
物作りには階層がある
まず、私がISA-95を知って目から鱗だったのが、機能の階層モデルという考え方です。
ISA-95には二つの階層モデルがあります。
- 機能の階層モデル
- 設備の階層モデル
機能の階層モデル
更に概念的に表すと以下のようになります。
各レベルのアクティビティの概要は以下です。
- Lv.4 (関連部門:営業、経営企画)
原材料、在庫、エネルギー使用量の管理、や製品の品質保証情報、サプライヤーの生産能力値等の管理を行う。生産基準計画(MPS)に基づき、保全必要性、設備稼働率等に基づいて生産計画を立案する。
- Lv.3 (関連部門:生産管理)
生産現場に近い立場から、ラインごとに詳細スケジューリングを行い、原価管理と費用の最小化を図る。作成したスケジューに基づきラインや設備の運転、移動管理を行いながら、必要に応じてスケジュール変更を行う。品質管理データの集計、統計解析、工程能力管理も行われる。
- Lv.2~0 (関連部門:生産技術、保全、製造)
生産セル、ラインごとにより細かい粒度でのプロセスを対象とする。管理・監視機能、設備オペレーションや制御機能、プロセスコントロール機能が実施される。
生産形態により、バッチコントロール、連続コントロール、ディスクリートコントロールに分かれる。ISA-95のスコープ外であり、このレベルのアクティビティは定義されていない。
設備の階層モデル
- エンタープライズ
サイトの集まり。設備に役割の最上位に位置する。
どの製品を製造するか、それをどのサイトで製造するか、総合的な経営判断を行います。
(例)本社機能
- サイト
エンタープライズを構成する物理的、地理的、論理的要素。エリアの集まりで、生産ライン、プロセスセル、生産ユニットを含む。それぞれのサイトで独自の生産能力を有する。
(例)地理的に独立した工場
- エリア
サイトを構成する物理的、地理的、論理的要素。
プロセスセル、生産ユニット、生産ライン、貯蔵ゾーンといったワークセンタが含まれる。通常、サイト内の地理的ロケーションや生産能力の種類によって識別される。それぞれのエリアで独自の生産能力を有するのが一般的。
(例)工場内の特定工程
- ワークセンタとワークユニット
設備の役割階層でエリアの下に位置する。
バッチ生産用設備はプロセスセル、連続コントロールに対応する連続生産設備は生産ユニット、ディスクリートコントロールに対応するディスクリート生産用設備は生産ラインと呼ばれる。また、生産形態に依らず、貯蔵や移動用設備は貯蔵ゾーンと呼ばれる。
(例)〇生産ライン、〇製造装置
各、生産分類についてもう少し深堀します。
- 生産ユニットとユニット
連続製造プロセスにおいて、製造オペレーションマネジメント(図1,Lv.3)が認識する最下層の設備。
生産ユニットはユニットから構成され、ユニットは装置モジュール、センサ、アクチュエータ、等の要素からなる。生産ユニットは自動化された連続生産に必要な全ての装置を取りまとめた単位であり、1つ以上の供給原料を変換、分離、反応させて中間製品、または最終製品を生産する。
- 生産ラインとワークセル
ディスクリート製造プロセスにおいて、製造オペレーションマネジメントが認識する最下層の設備。
一般的に自動化された一連のプロセスを行う単位であるが、手作業が入る場合はワークセルに相当する作業ステップを柔軟に組み替えることが可能。生産ラインとワークセルはそれぞれ、設備ごとに製造能力や許容量データを持つ。
- 貯蔵ゾーンと貯蔵ユニット
原材料、製品在庫を保持する機能において、製造オペレーションマネジメントが認識する最下層の設備。
貯蔵ゾーンでは受領、貯蔵、取り出し、移動、出荷が実施される。さらに、エンタープライズ内外を問わず、ワークセンタ間で原材料を移動することもあります。貯蔵ユニットはの物理的ロケーションは運送中の場所、時間によって変わることもある。
以下は、三菱ケミカル鹿島コンビナート内のエンタープライズ群です。様々な企業がパイプラインで繋がっていることが分かります。
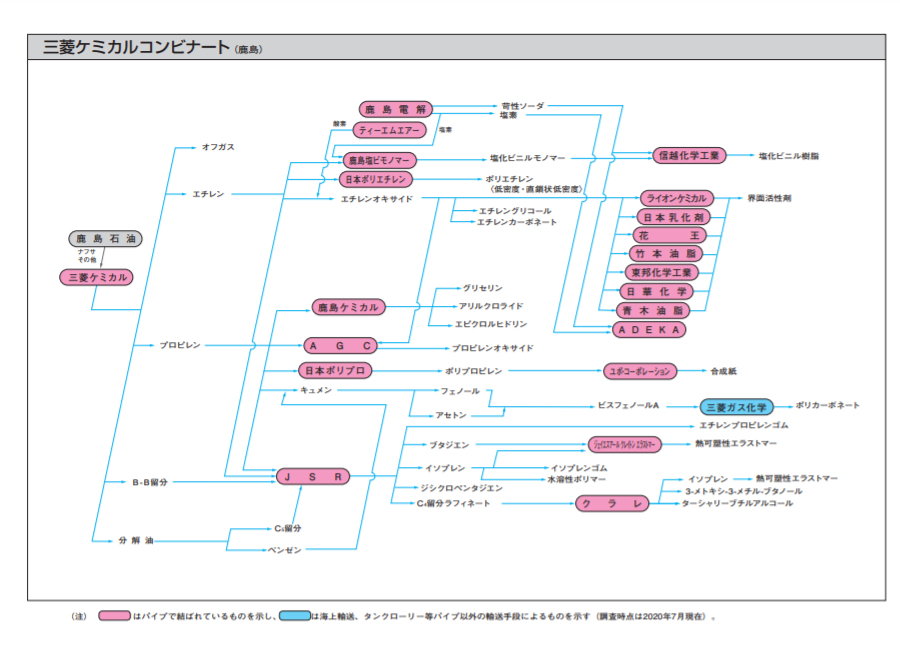
図3:三菱ケミカル鹿島コンビナート(出典:https://www.jpca.or.jp/files/trends/kakusha.pdf#page=4)(クリックで拡大)
- バッチプロセス(batch process)
一つ以上の設備を用いて,有限時間の間に有限量の入力物質を供給し,順序付けられた一連の処理を行うことによって,有限量の物質を生産するプロセス
連続プロセス
物質は連続した流れとして処理設備を通過する。一度安定した操業の状態が確立されると,プロセスの性質は,操業時期に依存しなくなる。立上げ,過渡状態及び立下げは,通常,計画された生産を達成することには寄与しない。
離散プロセス (ディスクリート)
製品は原料の種類,生産要件及び生産履歴に基づく生産ロットによって分類される。離散プロセスでは,加工ステーション間を指定された数の部品が一つのグループとして移動する。しかし,グループ内の個々の部品は区別することができる。
12個の機能群で物作りを俯瞰して見る
ISA-95では、エンタープライズ(図2参照)を12の機能群に分類しています。
この図が非常に分かり易いので引用させていただきます。
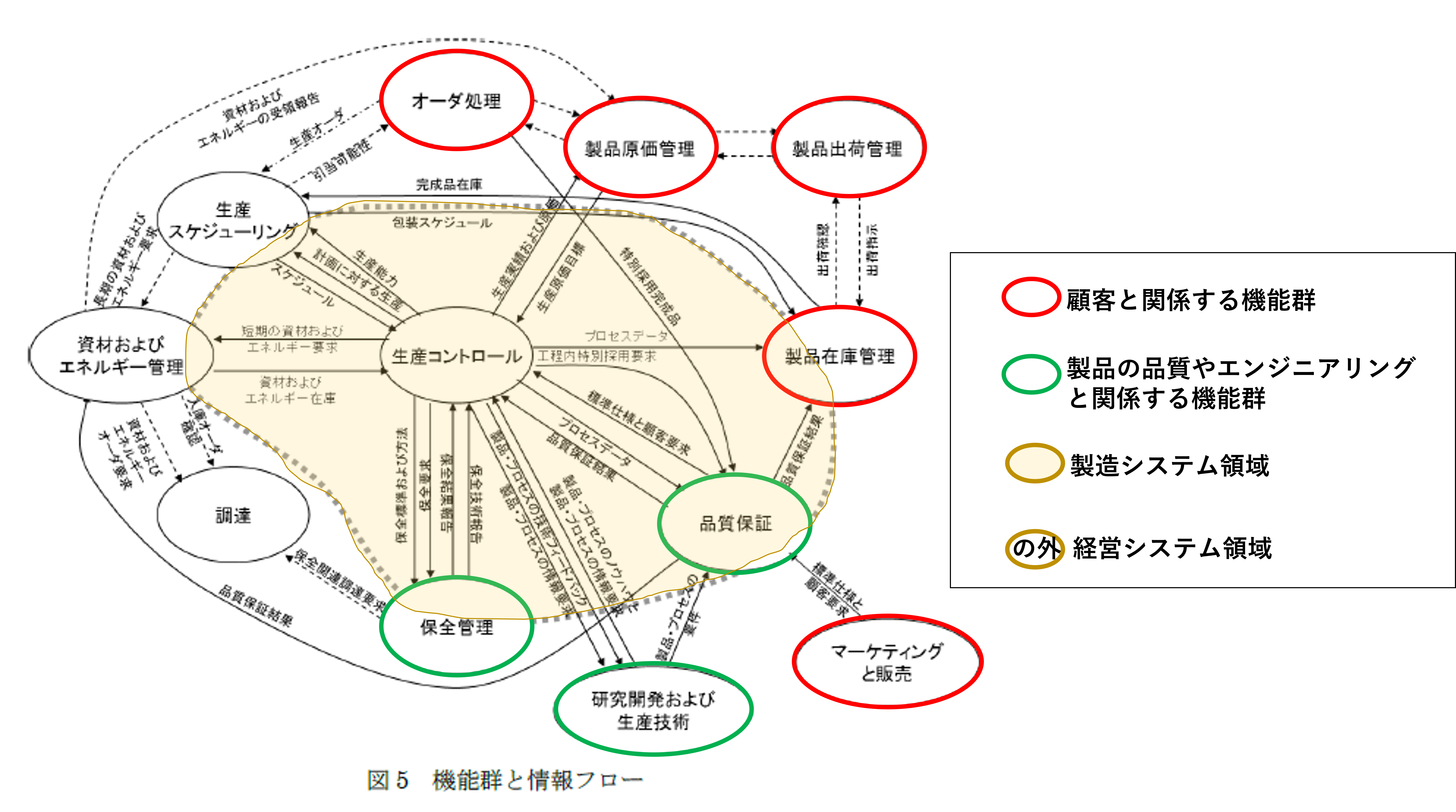
図4:エンタープライズを構成する12の機能(出典:http://apsom.org/docs/2015/20150323poms.pdf)(クリックで拡大)
これら機能群には、図1の機能階層モデルのLv.3、4が混在しています。赤枠は顧客と接点のある機能、緑枠は品質や開発に関わる機能です。
そして、黄色ハッチング部が製造システム領域、それ以外が経営システム領域になります。製造システム領域と経営システム領域を柔軟に連携させることが、多くの企業にとって重要課題です。そして、これは昨今話題のカーボンニュートラルに対応していく観点でも重要と思われます(※後述)。
また、各機能の間の情報(データ)のやり取りを線で表しています。この情報連携を円滑に行うことが、物作りのおけるデータ活用を加速させると思われます。
特に重要なのが、中央の「生産コントロール」です。これは、図1.Lv.3の「製造オペレーションマネジメント」に関連する機能になります。
生産コントロール機能の中身
多くのメーカーで機能間の人的交流がないのではないでしょうか?私は緑枠の領域のデータサイエンティストをしていますが、マーケティングやエネルギー管理などの領域にも進出したいと考えています。
私は仕事でプロセスデータを用いて、不良要因解析を行うことがあります。
不良モードや発生箇所とプロセスデータを紐付けて、どのような製造条件の時にどのような不良が発生し易いか?をデータから検証します。その際、図4の生産コントロールと品質保証領域が連携していないと、プロセスデータと品質検査の結果が紐付きません。このような場合、人手で紐付ける必要が生じます。しかし、図1 Lv.3にあたるMESが導入されていれば、以下の図のように工程を跨いだ要因解析も容易になると思われます。
次に「製造オペレーションマネジメント」の観点で俯瞰してみます。
図4と同様、黄色ハッチング部が製造システム領域、それ以外が経営システム領域になります。
灰色ハッチングは、製造オペレーションマネジメントを構成する4つの管理項目です。
- 生産オペレーション管理
生産オーダーに対して、部品や製品を生産するためのアクティビティを扱います。原材料、エネルギー、設備、作業者、情報を利用して、コスト、品質、生産量、安全性、納期を考慮しながら、調整、指示、管理、トラッキングを実施。ワークセンタに対して実行される生産に関する全てのアクティビティを含む。
- 保全オペレーション管理
ワークセンタ、ワークユニットを構成する設備を、生産可能な状態に維持するアクティビティを扱う。設備、ツール、関連施設の保全を行い、それらが確実に使える状態にしたます。緊急トラブル対応、定期メンテナンス、予防保全、それらのためのスケジューリングを行う。過去のイベントや問題の履歴を管理、装置の性能、作業者実績、計装の信頼性の問題診断に役立てます。
- 品質オペレーション管理
品質の測定や報告機能を調整、指示、管理、トラッキングするアクティビティを扱う。製造オペレーションマネジメントでは、製品の品質保証と注意すべき問題点の特定を行うために、製造からリアルタイムデータの収集や分析と言った機能が提供され、関連症状や対応とその結果を収集します。また、品質検査結果をトラッキングし、統計的品質管理(SQC)を行うアクティビティがあります。
- 在庫オペレーション管理
在庫や資材の移動を調整、指示、管理、トラッキングするアクティビティを扱います。在庫オペレーションは、適正な在庫レベルの設定や、入庫・出庫管理、在庫棚卸、資材ピッキング、搬送、工場間のワークの移動などを行います。
製造オペレーションマネジメントでは、セキュリティの管理、情報管理、文書管理など、様々なアクティビティが存在します。しかし、ISA-95では、それらのアクティビティについては規格として定義していません。
最後に、製造オペレーションマネジメントを主要な情報の流れとして俯瞰してみます。
大きな流れは、ERPなど経営システム領域から降りてくる(図6、青太矢印)フローです。この指示と、リソース管理が持つ情報を加味して「詳細スケジューリング」が作成されます。
この詳細スケジュールに基づき、ディスパッチングが作業をディスパッチし、更に「定義管理」から製造方法などの情報を入手して「実行管理」が作業実行を指示します。
製造実行の結果は「データ収集」に集約され、「パフォーマンス解析」や「トラッキング」を経由して、オペレーションレスポンスとして再び経営システム領域に戻されます。
1つ1つの作業について説明します。
- 詳細スケジューリング
それぞれの設備、製品の特性に応じて異なる優先度、属性、生産ルールに基づいて、作業順序を決定します。作業順序を適正化することで、段取りの最小化やスループットの最大化に繋がります。ここでは、資源の能力量が有限であるこを前提に負荷の分散やシフトパターン調整を行い、代替作業や並行作業を検討します。
- ディスパッチング
計画されたジョブオーダ、バッチ、ロットなどを、特定設備や作業者へ割り当てることで、生産現場におけるオペレーションの流れを管理します。詳細スケジュールを、許容された制限の中で、ローカルな個々の能力や製造条件に応じて変更します。また、仕掛品や再投入品のコントロールも併せて行います。
- 実行管理
生産、保全、品質、在庫などカテゴリごとにジョブリストにある内容に従って、直接リソースをコントロールし、その実行結果を得ます。ロットやサブロットやバッチの個々単位を実行し、正しい操作手順で作業を完了させ、現物のとしての製品を生産します。ただし、実際の具体的なワーク内容に関しては、Lv.2の領域でコントロールします。
- リソース管理
作業者、設備、資材などが定義されている。これらの性能データ、保全データ、原価データなどが管理対象となる。また、管理だけでなく、各種リソースの予約を行います。また、設備の段取りおよび状態管理や稼働履歴の管理も行います。
- 定義管理
ワークセンタごとに定義されている生産ルールや各種書式を管理します。例えば、レシピ、図面、SOP、NCプログラム、バッチ記録、シフト間連絡書などがあります。さらに、法規制文書、環境、安全衛生の規則文書などの管理と整合性維持を行います。
- トラッキング(いわゆる、トレサビ)
生産状態やワーク処理に関する情報を提供する。ワークに割り当てられた作業者、材料ロット、アラーム情報、その他例外事項も含みます。ここでは、最終製品について、構成品の種類や使用量の情報を記録し、後の製品情報のトレースを可能にします。
- データ収集
設備の運転データや各種パラメータを取得します。同時に設備や生産プロセスのリアルタイムな状態や、生産、保全、品質、在庫に関するデータの履歴を提供する。
- パフォーマンス解析
不具合の改善のために、製造オペレーションマネジメントに関わる様々な指標のパフォーマンスを解析します。実際のパフォーマンスを分単位で更新し、計画と比較します。パフォーマンスとは例えば、可動率、能力余裕、サイクルタイム、生産の計画達成率などがあります。
製造システム領域と経営システム領域を上手く連携した例が、「旭鉄工株式会社のIoT経営ダッシュボード」だと思います。
興味がある方は以下の動画を参照ください。
カーボンニュートラル時代にはISA-95が重要!?
製造業では(製造業でなくても)、これからの時代はカーボンニュートラルへの対応が必要になります。カーボンニュートラルへの対応ができていないメーカーはサプライチェーンから除外される可能性があります。
そこで重要になってくるのがカーボンフットプリントという概念です。
カーボンフットプリントとは「製品に使われる原料の製造 ⇒ 製品製造 ⇒ 製品の使用 ⇒ 製品の廃棄」まで、その製品のライフサイクルで発生するCO2をトレサビしたものです。
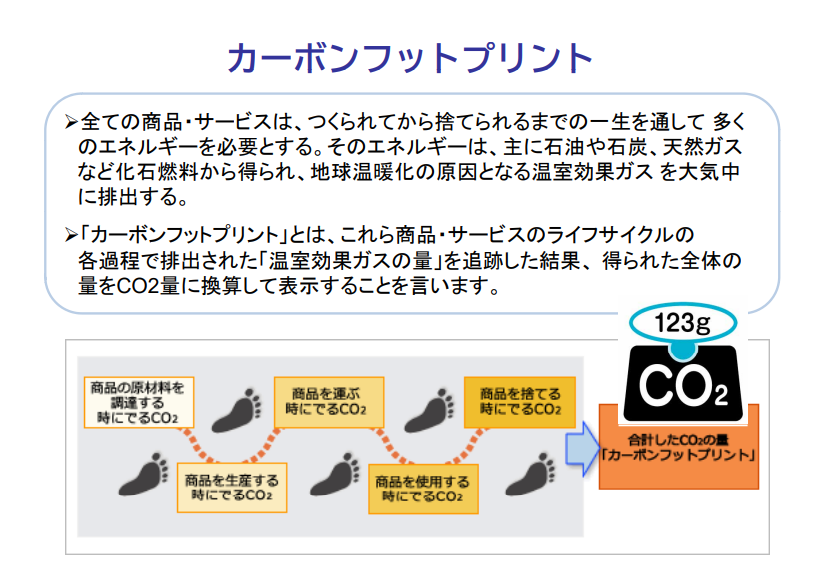
図8:(出典:環境省資料)(クリックで拡大)
ISA-95とカーボンニュートラルがどう関わってくるのか?
私が関連を考えるようになったのは、(独)化学大手BASFが全製品のカーボンフットプリントを提供すると発表したことからでした。
また、欧州の電池産業で、2024年より製品の製造・廃棄時にカーボンフットプリントの表示義務が課せられるというニュースからです。
さて、カーボンフットプリントの把握は自社内だけトレサビすれば事足りるのでしょうか?
いいえ、サプライチェーン全体を含めて追跡・計算することが求められる可能性があります。以下、環境省発行の資料が良くまとまっていましたので、興味がある方はご覧ください。
サプライチェーンを含めると、CO2排出量を計算しないといけない範囲がかなり広範囲に渡ります。
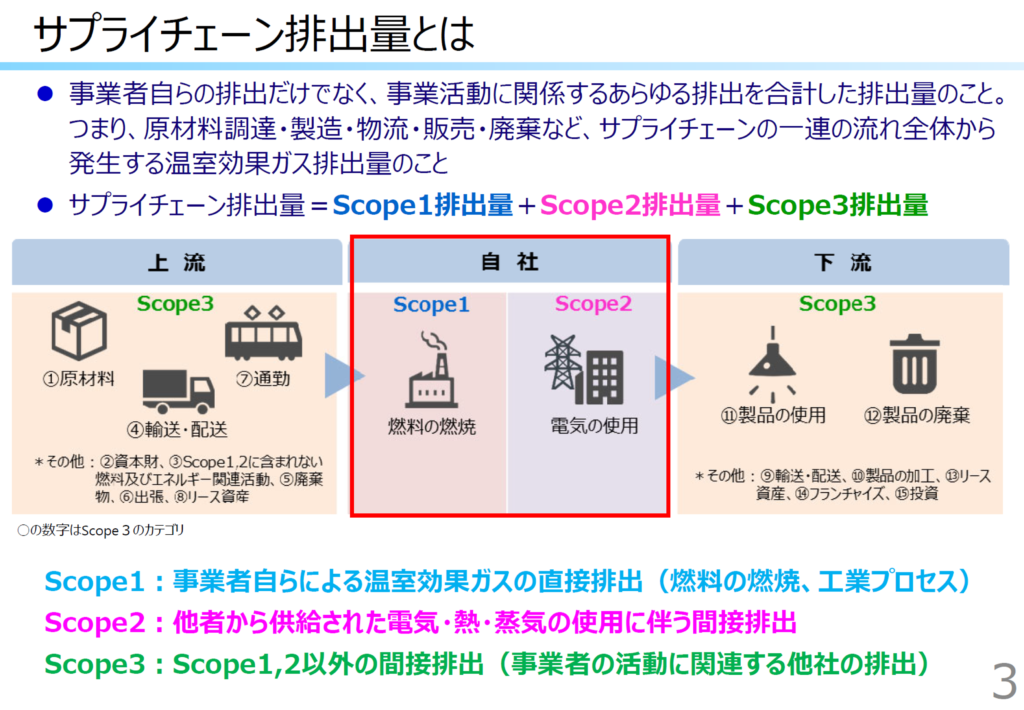
図11:サプライチェーン排出量 (出典:環境省資料) (クリックでリンクに飛びます)
自社だけでなくサプライヤーを含めて管理が必要となると、図1のレベル0~4の連携が必要になると思われます。
特にレベル3のMESによる自社工場内での排出量管理と、レベル4のERPによるサプライチェーンを含めた排出量管理が重要になってくと思われます。
レベル3以上の仕組みがないと、カーボンフットプリントの算出に多大な工数がかかることや、そもそも算出できず、サプライチェーンから締め出される懸念もあると考えます。
現時点で、製品単位でのカーボンフットプリントの提供がグローバルスタンダードになるか?は、不明です。が、その可能性は考慮しておいた方が良いと思われます。
以下の動画の18:00からの内容が参考になりました。こちらのついては政治的な動向をウォッチしていこうと思います。
ISA-95で定められた工場系KPI
ISA-95を勉強する過程で知った、物作りに関するKPIをついでに紹介します。
ISA95を参照している、ISO22400という規格で34のKPI定められています。
これらの指標の中に今後、CO2排出量など、カーボンニュートラル関連の指標も入ってくるかも知れません。
工場へのAI実装時には、要件定義の段階で「どのKPIを達成することが目的なのか?そして、その達成責任はどの部門にあるのか?」を明確化しておくことが大切です。でないと、PJが迷走することになります💦
参考資料
記事作成に使用した資料を紹介します。分かり易い資料ばかりでISA-95を勉強するのにおススメのものばかりです。
- ものづくりAPS推進機構
製造オペレーションマネジメント入門 ~ISA-95 が製造業を変える!~
これは外せないです。日本語で書かれた解説書で一番分かり易いのではないでしょうか?初めに読まれることをおススメします!
- ダッソーシステムズ株式会社
スマートマニュファクチャリングの実現に向けた工場のデジタル化 ― ISA-95の考え方とMES/MOMの構築方法 ―
MOMの代表的ベンダーである、ダッソーシステムズがISA-95と関連製品について書いた記事です。コンパクトかつ、図が多用されているので非常に理解し易いです。
上記と併せて読まれることをおススメします!申し込みフォームから入手可能です。
<生産管理システム全般>
生産管理を学ぶ初めの1歩はこちらがおススメ。
石川和幸 エンジニアが学ぶ生産管理システムの「知識」と「技術」翔泳社; 第1版 (2021/4/19)
<用語集>
ISA-95界隈では、MES、PLC、SCADA、ERP、、 と耳慣れない用語が頻出します。各用語がどういった意味なのか?を理解するために以下の資料が大変役立ちましたm(^^)m
- アーサー・ディ・リトル・ジャパン株式会社
サイバーフィジカルシステムの戦略的導入等に係る調査
- 化工リーマンさん(@kako_riman)のブログ
SCADA、DCS、PLCの違い